|
|
- Description
- Features
- Benefits
|
The MSC I™ is a microprocessor based stepper motor controller which provides a 1/10 micro stepping output to operate most stepper drive motors requiring 1.0 – 6.5 amps/phase current. The controller is designed to be used with the CWT torch positioning slides and the CWT weld sequence controller. It can also be used as a stand-alone positioning controller. The MSC II has an isolated RS-485 port, which can be configured to allow off-line programming and control of the stepper motor. The MSC II can be configured to use the Local Area Network (LAN) port which allows the CWT weld sequence control to program and control the CWT torch positioning slide assemblies.
The MSC II provides a constant current Sine/Cosine output to operate two-phase stepper motors. The output phase current can be user programmed from 1.0 – 6.5 amps. In the 1/10 step mode each step of the motor is subdivided into 10 micro steps. When using a 200 step/revolution motor the MSC II will provide a 2000 step/rev output at a maximum speed of 240 rpm.
The MSC II controller should be located near the stepper drive motor it is controlling. The maximum motor drive cable length is 75 ft. Mount the MSC II controller in a location that allows easy access to the front and rear panel. Figure 2-1 shows the mounting pattern for the control enclosure.
The MSC II provides two limit switch inputs, which are used to prevent over driving the mechanical slide assembly and to establish a home position. The MSC II provides a power down brake output, which can be used to operate a electro-mechanical motor brake.
The MSC II is designed for use with Computer Weld Technology's controller using serial LAN communication or it can be configured for use through a standard RS-485 serial port using ASCII serial commands. It can also be configured to use Modbus RTU protocol over the RS-485 serial port. |
|
|
|
Product Specifications |
|
|
Dimensions |
4.75"h x 2.0"w x 11.0"l (120.6mm x 50.8mm x 279.4mm) |
Mounting Dimensions |
1.25" wide x 10.25" long, four 0.25” diameter hole |
Weight |
4 lbs (1.18 kgms) |
Power Input |
120 ± 10% vac 50/60 hz @ 5.0 amps |
Operating Temperature |
-10° F to +140° F (-23° C to +60° C) |
|
|
Motor Output Current |
1.0 - 6.5 amps peak each phase |
Motor Output Voltage |
1.5 -18.0 volts peak each phase |
Current Profile |
Sine/Cosine |
Limit with Inputs |
CW and CCW 5.0 vdc active low inputs with internal 4.7K ohm pull up resistor |
Brake Solenoid Output |
24 vdc @ 0.5 amp for 0.5 seconds then 2.0 khz PWM modulated for 12 vdc hold-in voltage @ 0.5 amps |
Step Resolutions |
10 micro steps/step |
Velocity |
10 - 8000 steps/sec. |
Acceleration |
10 - 1000 steps/sec² |
Index step count |
1 - 65535 steps |
Index Scale Factor |
1-255 steps/step scale factor |
Communications |
Isolated RS485 19,200 Baud Modbus RTU port |
|
|
|
|
|
|
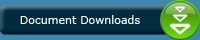 |
|
|
Please disable browser pop-up blockers for documents on cweldtech.com to allow PDF files. |
|
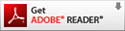 |
Note - All documents are in an Adobe PDF file format. |
|
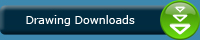 |
Press to enter download area for Autocad DXF drawing format. |
|
|